One such advancement is in inventory management or stock-taking – a crucial factor in retail stores' success.
In pursuit of retail excellence, Mediaset introduces Traze's unified approach to inventory management by integrating RFID technology. The introduction of Radio Frequency Identification (RFID) into retail has shown a new era of automation and precision, eased the burdens of traditional stock-taking and redefined the retail landscape as we know it.
This is a journey to uncover the unparalleled advantages of utilizing RFID systems in retail and discover how Mediaset's collaboration with Traze is changing the way retailers approach today's inventory management processes.
Embrace the possibilities as we witness firsthand how this unified solution automates your retail store to meet and exceed modern consumers' expectations.
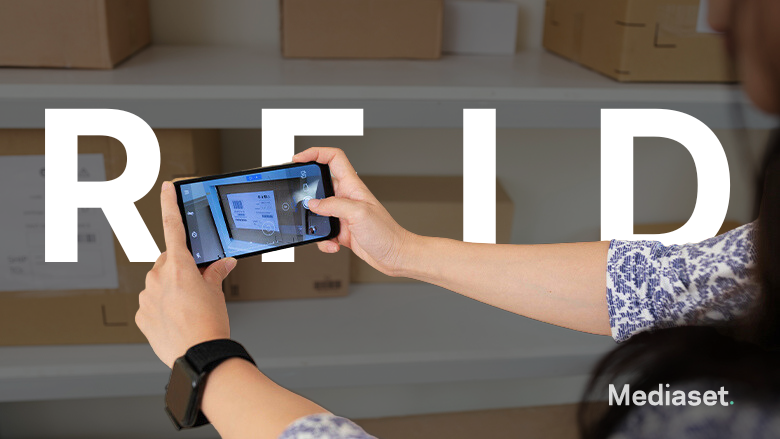
Understanding RFID Technology
Radio-frequency identification (RFID) technology may seem like a futuristic concept but it has been integrated into various systems in different industries including retail.
In its essence, the RFID system uses radio waves to identify and track objects equipped with active RFID tags or smart tags. These RFID tags consist of a small microchip and an antenna which together enable them to transmit data collected from RFID readers when activated by radio waves.
To have a closer look and understand how this functions in bigger areas in the retail industry, discover how each fundamental components of an RFID system operate:
RFID tags
The RFID tag can be attached to products, packaging, or embedded into items during manufacturing.
The data stored on multiple RFID tags can range from unique identifiers to more detailed information about the product such as its manufacturing dates, batch numbers, and expiration dates– used for determining inventory levels.
RFID tags are also attached to allow for automatic data capture and transmission. However, only active RFID tags have a power source that allows them to transmit accurate data over longer distances.
RFID readers
This device is responsible for transmitting and receiving radio waves to communicate with the RFID tags. When the RFID tags enter the reader's range, it detects the tags' signal and captures the encoded data.
Depending on the inventory system, the specific RFID readers can be fixed or handheld, providing retailers with flexibility in implementing RFID technology throughout their store and warehouse operators.
Integrated software
The RFID data collected by RFID readers is sent to a backend software where it is processed and stored. Retailers can access this to gain real-time insights into inventory levels, manage inventory counts, and optimize inventory check-in.
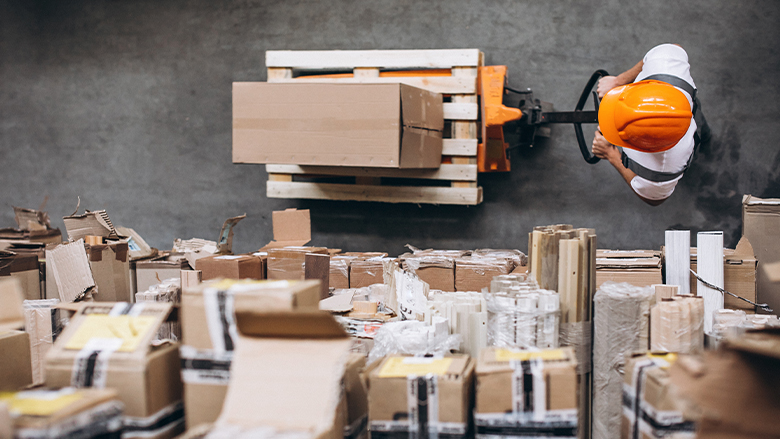
Challenges faced over traditional inventory processes
While the traditional inventory management process has served well in the past, it also comes with various challenges that can slow down productivity, accuracy, and operational performance.
These challenges can result in costly stockouts or excess inventory impacting customer satisfaction and store profitability.
The reliance on manual data entry
one of the most significant challenges in the traditional way of doing inventory management. From recording inventory levels to asset tracking, human involvement leaves room for errors leading to discrepancies in inventory tracking, misplaced items, and poor inventory visibility.
Time-consuming inventory management processes
Also, the physical counting of items can take hours and worst- days, particularly in large retail stores. As businesses grow, inventory levels increase, and this time-consuming inefficiency becomes more pronounced that it slows down operations and blocks the ability to respond quickly to market demands.
Processes of traditional inventory management often provide limited data insights
Basic inventory levels and movement data might be available, but they lack the depth and complexity required to gain valuable insights into consumer behavior, purchasing patterns, and inventory tracking bottlenecks.
Costs and wastes
The traditional inventory tracking approach can suffer significant costs over time. Expenses related to paper-based record-keeping, physical audits, and the labor costs of these processes can add up.
Inventory management security
Retailers may put their businesses at risk for financial loss and compromised supply chain integrity because barcode labels can be replicated, and manual records are exposed to tampering or loss.
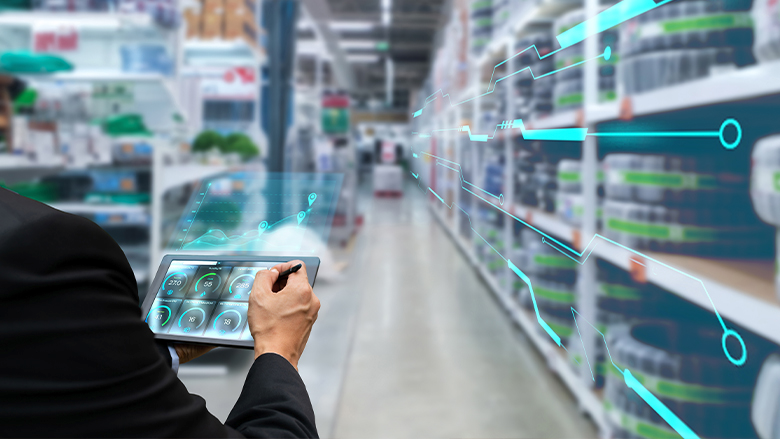
What sets the RFID inventory system apart from traditional barcode systems is its ability to communicate wirelessly
The key differentiator lies in the method of data capture. The traditional scanning of barcode labels and QR codes requires physical nearness and direct visibility, leading to time-consuming processes, especially if a store is in a large-scale inventory management system.
Unlike barcode scanning which requires line-of-sight and manual counts, the RFID inventory management system allows for non-contact and simultaneous identification of multiple items even when they are not within the direct line of sight of the RFID reader.
As products move throughout the supply chain and within the store, the RFID reader instantly captures and updates the item's location and status in the system.
At its core, RFID technology automates inventory management through a seamless and real-time inventory check system that significantly enhances accuracy, visibility, and decision-making capabilities.
These features have unlocked a large scope of possibilities in current inventory management systems restructuring how retail stores handle stock control and asset tracking.
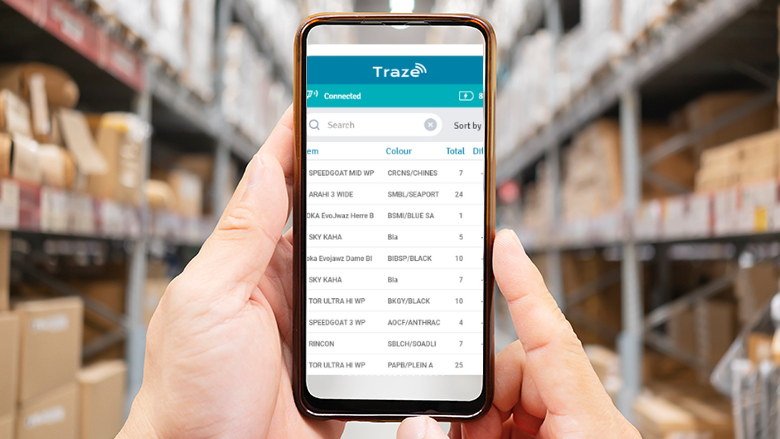
Traze's structured RFID inventory management system
Imagine running a store with the right technology that is cost-effective letting your customers pick up items from the shelves then your retail store's inventory system automatically updates in real time. No more manual inventory checks or time-consuming stock scanning through your physical inventory.
Welcome to the unified future of the new inventory management process.
With a focus on saving time, and ensuring simplicity and efficiency, Traze developed a user-friendly solution that is undoubtedly at the forefront of reshaping retail for the better. Utilizing RFID tags attached to each product scanned by the RFID reader, Traze's RFID inventory tracking solution enables a seamless flow of items throughout the entire supply chain, from the shipment verification to the retail shelves and ultimately into the hands of customers.
The RFID tags can be quickly affixed to products, and the intuitive user interface ensures that store personnel can begin using the system with minimal training. This streamlined integration means retailers can start reaping the benefits of Traze's solution almost immediately, without any significant disruptions to their day-to-day operations.
Enhanced inventory visibility
As customers pick up items from the shelves, RFID tags communicate with the store's embedded inventory management system then automatically updates the stock levels– real-time stock control.
This real-time data empowers store managers to monitor inventory levels accurately and make informed decisions on restocking and replenishment through a dashboard on their mobile phones or any handheld devices based on real-time asset counts. As a result, the risk of products running out of stock during peak demand periods is greatly minimized, leading to increased customer satisfaction and faster turnovers.
The increased transparency also facilitates better collaboration between your employees as it can support all kinds of goods-handling processes between stores resulting in inventory accuracy and reduced labor costs.
Seamless integration with existing systems
When it comes to adapting new technologies in enhancing inventory management leaves a fear of disruptions and complicated integrations which can prevent retailers from upgrading the system. However, Traze's future-proof solution of utilizing an RFID inventory management system is designed with scalability and compatibility in mind.
You can seamlessly integrate your existing systems such as your store's point-of-sale systems, providing an excellent operational transition to complement and enhance your current setup.
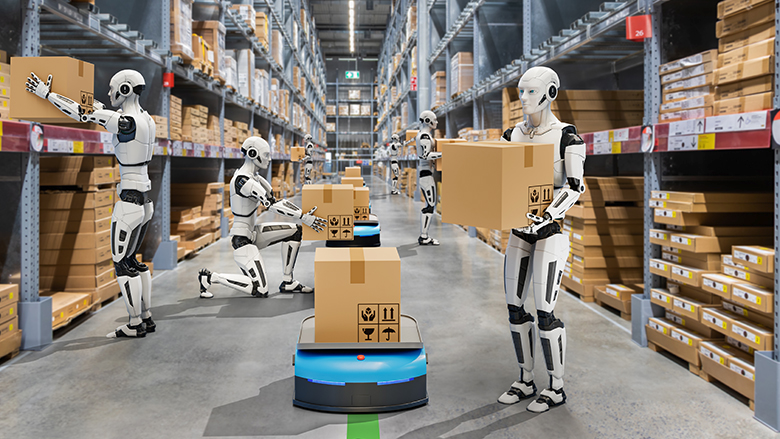
The lasting impact on the retail landscape is the time to harness advancements today!
With the retail industry constantly evolving, now is the time for retailers to harness technology with the RFID system and other advancements in inventory management.
Embracing these innovations will not only revolutionize operations but also enhance the overall customer experience. As Mediaset and Traze continue to collaborate, the retail landscape will witness further advancements and improvements that can redefine the way retailers approach inventory management, ultimately shaping a more efficient and customer-centric retail environment.
Innovation is here, and it's time for you to embrace the possibilities of advanced technologies and show in a new era of RFID inventory management excellence– a transformative force that will continue to shape advanced inventory transactions for years to come.
Be better equipped to navigate the challenges of today and set new standards for operational excellence and customer experience for tomorrow.