At the forefront of this transformation, Mediaset seamlessly uses advanced technologies with retail operations to optimize the inventory management process and other retail store areas.
The pressure to deliver exceptional customer experiences while maintaining very small margins is more pronounced than ever. The traditional approaches to the inventory management system, marked by manual inventory checks, manual inventory counts, and outdated asset tracking methods, are filled with challenges that impact operational efficiency, cost, and the bottom line.
According to retail industry reports, issues like overstocked shelves leading to increased carrying costs and wastage, out-of-stock items causing missed sales opportunities, and inaccurate inventory counts triggering order fulfillment discrepancies collectively contribute massive losses amounting to approximately 10% of revenue on average for retailers.
In this article, we'll provide you with information about the real challenges and help you learn how Mediaset can reduce these numbers by significantly reducing the cost of labor while utilizing the RFID inventory management system.
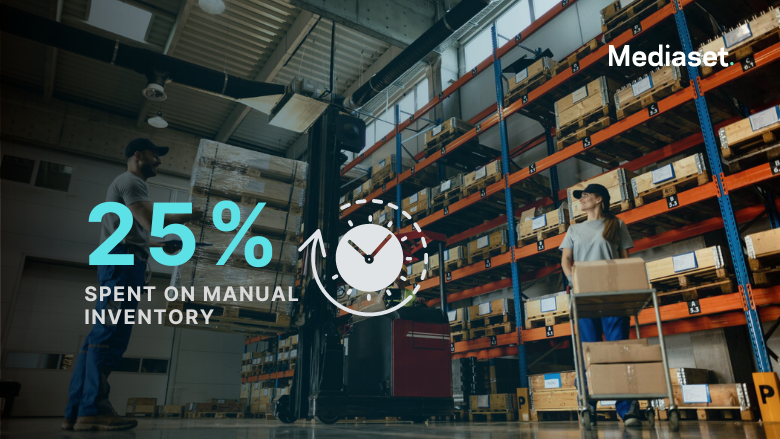
The real challenges with an increased labor cost associated with manual inventory management...
The power of digital transformation is not just about embracing the latest technologies– it's about mitigating the tangible challenges that arise from sticking to conventional inventory management methods.
Inaccuracy with quality control
Imagine a retail store that is facing challenges in maintaining inventory accuracy in sync with consumer demand.
Shelves are often either overloaded with excess stock or frustratingly empty due to underestimating popular items.
This results in employees being slowed down by time-consuming manual inventory counts, stock control, and inventory adjustments, causing operational efficiency to suffer, and labor costs to continue to escalate.
Manual cost of labor
Research suggests that up to 25% of employees' time is spent on inventory-related tasks when manual methods are employed. What if we maximize these hours for customer engagement and other high-value activities that drive revenue to the store?
Time sensitivity + Waste
Accurate shelf-life tracking is necessary for retail stores with perishable goods constantly nearing expiration, as poor tracking can lead to excessive markdowns.
The complex hop of supply and demand becomes increasingly complicated as inaccurate inventory levels hinder the ability to replenish shelves at the right time.
Overstocking due to inaccurate demand forecasts results in excess inventory, contributing to higher storage costs and increased risk of outdated products. Hence, understocking drives retailers to implement faster shipping methods, further inflating operational expenses.
Equipped with Radio Frequency Identification in inventory tracking
The solution includes that each item is equipped with active RFID tags, which transmit data via RFID readers' radio waves placed strategically throughout the store.
RFID technology offers constant visibility to the supply chain process, from distribution centers to warehouse operators to shipment verification to inventory check-in.
As products move throughout the tracking process, RFID tags are captured for real-time asset counts, empowering retailers to respond quickly to store challenges.
Advanced inventory transactions
Based on the record, retailers implementing advanced RFID inventory management systems with their existing infrastructure can reduce labor costs by up to 20%.
Why?
The automation of data capture and data collection ensures that employees spend less time on manual stock control.
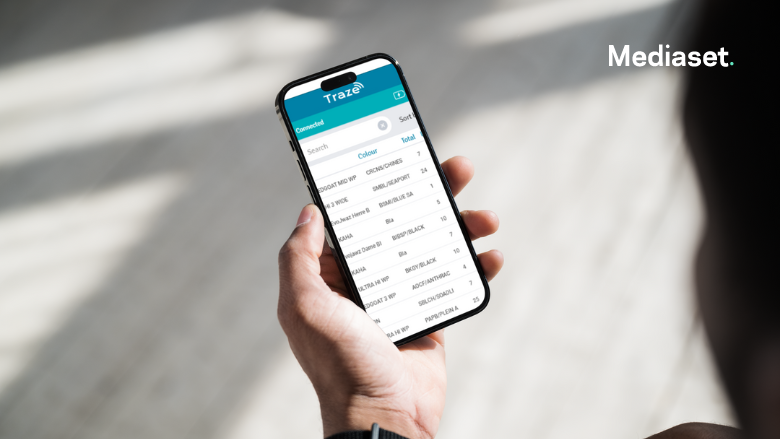
Mediaset's real-time solution in reducing labor costs and other unnecessary resource wastage
Partnering with Traze, developed a real-time solution that utilizes RFID technology for data collection, inventory accuracy, and a cost-effective retail environment.
Discover how the RFID system works in different areas in tracking inventory, which consumes the most labor and resource wastage.
Retail stock control
Traze's RFID inventory system eliminates much of the time required for stock-taking, reducing labor costs associated with manual data collection and verification.
Supply chain
Traze has its own approach to handling RFID tags on items at different stages of the supply chain process. From manufacturer to wholesaler to store. This ensures your seamless tracking from production to sale.
Order picking
The solution recommends a batch-picking approach to transform your process into a highly efficient operation. For missing items, RFID systems enable specific RFID readers in your store to locate items with the RFID tag to minimize time wastage – enhancing labor efficiency!
Goods handling processes
With Traze's support of a real-time visibility dashboard for retailers, you can accurately manage transfers between stores to return to distribution centers back to suppliers.
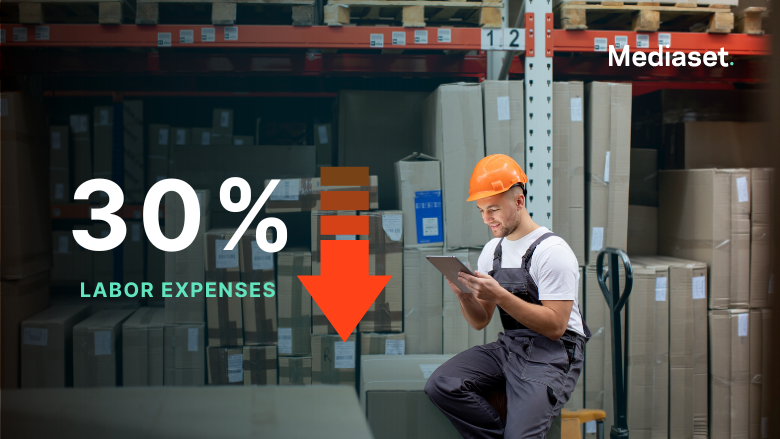
Impact of reduced labor costs
Countless hours spent on manual inventory can now be repurposed for high-value store operations, resulting in retailers experiencing a multiplier effect where reduced labor costs directly translate into increased inventory efficiency and revenue generation.
Retail success stories have emphasized the deep impact of reduced cost of labor through RFID technology.
They have reported a significant drop in labor expenses, achieving up to a remarkable 30% reduction.
Does this mean reducing manpower?
The reduction in labor costs achieved through Traze's embedded RFID technology doesn't necessarily mean reducing manpower. Rather, it involves a strategic reallocation of manpower.
Traze aims to automate many of the labor-intensive tasks with manual inventory management to free up employees from those tasks.
In essence, their utilization of RFID technology doesn't result in fewer employees, but instead, a reduction in labor costs enables retailers to shift their workforce towards more valuable and customer-centric tasks.